Technology in Manufacturing: The Modern Problem Solver
Brian Scott
When Henry Ford imagined the assembly line in 1913, little did he know just how far manufacturing would shift from hands-on work to technology-driven production, changing the way, shape and form that manufacturers build their products.
Fueled by artificial intelligence and machine learning to predictive maintenance and robotics, technological innovation for manufacturing operations is moving at a breakneck pace. While the lure of the latest-and-greatest technologies in the market can be scintillating, the questions abound about the necessity, cost and impact of upgrades and whether they’re right for the business.
While articles about trends in the industry and understanding when it’s time to invest have tackled the first two considerations, the third – the impact of investments – is critical to consider.
Most businesses would be hard-pressed to say their business doesn’t rely on technology. Everything from office equipment and tracking software to actual heavy machinery has been affected by the advances – often in leaps and bounds – that tech has brought to the forefront. With that in mind, it’s important to understand that in today’s age, technology can go beyond just producing outputs and instead help solve one of the most pressing problems in the business world today – a shortage of skilled employees.
A study conducted in 2021 by Deloitte and The Manufacturing Institute revealed that more than 2.1 million jobs could go unfilled by 2030, cost potentially $1 trillion.
The results are backed up by Dr. Christopher Thornberg of Beacon Economics, a leading economist. At a recent Economic Forum event, he pointed to pain points being experienced by today’s employers – namely the fact that there are more open positions to fill than there are employees partially due to the great resignation, but also the big retirement where labor market growth is stagnating and causing headaches, especially in the manufacturing field.
One answer to easing the labor shortage burden can be found by using productivity enhancements that come through capital investments.
1. Lighten the Load
While historically automation and technological improvements have been seen as threats to employee workforces, in today’s environment, they’re looked to as a relief for workers who find themselves doing double duty just to keep up with current production demands. From automated shrink wrappers to autonomous mobility that transports goods around an operation, a wide variety of technologies are being incorporated into the workforce to help reduce the number of positions an employer needs to fill.
And while the initial investment in upgrades can be significant, over the long-term, new equipment can help increase production while driving down employment costs, which stretch beyond salary into creating benefits and other personnel-related cost savings.
2. Increase Efficiency
Capital equipment improvements are known to increase reliability and productivity. As an added benefit, new technologies are increasingly incorporating built-in measurement tools that have the ability to give businesses real-time data and increased transparency when it comes to understanding processes, flag issues and show where efficiencies can be found to boost productivity, all without needing to invest valuable employee hours in tracking or data entry.
Additionally, many newer pieces of equipment are self-regulating and, much like a vehicle with a tire pressure or check engine light, will indicate where a potential problem exists, reducing in-depth diagnosis and decreasing the reliance on the specialized knowledge of already short-handed maintenance teams.
3. Maintain Real-Time Information
In addition to boosting productivity, newer equipment also has the ability to forecast challenges, plan distribution, manage supplies and more, all without needing hands-on attention or analysis, instead deploying those human resources to more critical functions within the operation. Additionally, with staffing shortages in transportation, business leaders can better organize loads, create more efficient shipment schedules and improve delivery by having a better handle on their internal operations.
While some manufacturers may struggle with the idea of making significant equipment upgrades in the short term, investments in operations can deliver myriad long-term benefits and mitigate the labor shortage, which shows no signs of abating.
Of course, weighing pros and cons, right-sizing investments and having a strategic growth plan are critical to ensure long-term competitiveness and viability in what can be an unforgiving environment. For this, reaching out to a team of experienced equipment finance specialists can reduce the burden and place greater peace of mind in being able to achieve long-term cost savings, increased productivity and often, the ability to take a company to the next level.
Western Alliance Bank’s expert equipment financing bankers have spent decades helping clients find the right options to meet the unique needs they face today and help plan for the future. Providing a 360° analysis, the team can help business leaders find efficiencies and right-size equipment investments. Through a personalized approach and dedicated relationships, the goal is to equip decision-makers with the tools and resources they need to make the best possible choice for their individual operations.
Brian Scott is managing director of Western Alliance Bank's Equipment Finance Team. He can be reached at [email protected] or 602.296.6649.
Equipment Finance
Western Alliance Equipment Finance, a national banking group within Western Alliance Bank, Member FDIC, delivers capital markets solutions in equipment financing for clients, wherever business happens. Its relationship banking experts blend in-depth experience in a wide variety of industries and sectors with responsive service and innovative banking options to help clients meet their goals. The Equipment Finance Group is part of Western Alliance Bancorporation, which has more than $80 billion in assets. Major accolades include being ranked as a top U.S. bank in 2024 by American Banker and Bank Director. With significant national capabilities, the Equipment Finance Group delivers the reach, resources and deep industry knowledge that make a difference for customers.
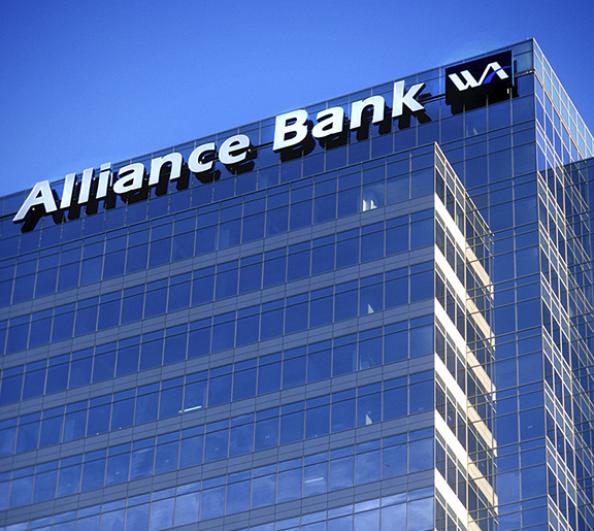